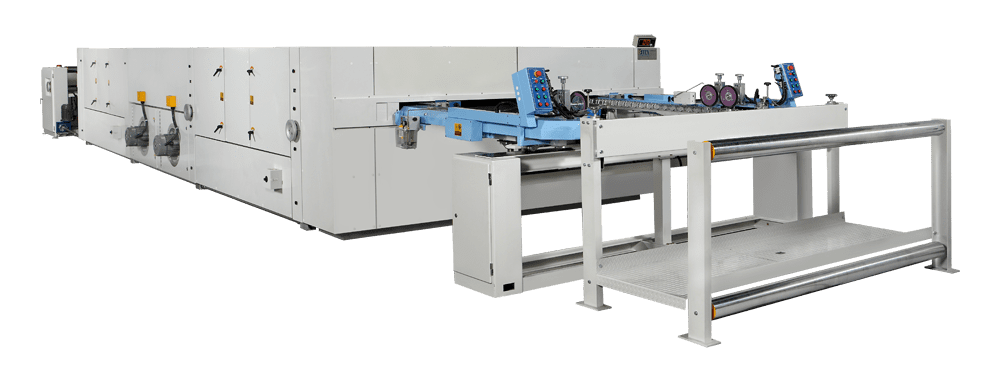
Heat setting reaction
By foaming, spraying or dipping process to let the chemical into the nonwoven fabrics which are initially solidified via physical process such as needle punch or spunlace. Fabric edge is fixed by pin plates and the size will be formed and stabilized by heat circulation flow. This process is by way of controlling hot air temperature, air volume, and reaction time to achieve the required physical and chemical properties.